Can Used Pallet Rack Meet Seismic Code?
- GRAFCO, Inc.
- Dec 8, 2017
- 2 min read
It depends…

and if so, who carries the risk?
Some say that all that’s needed for rack to meet seismic code is oversized footplates. This is an urban legend and only reflects part of the story.
What’s required to meet the code?

The design requirements for pallet rack structures are defined by the Rack Manufacturers Institute (RMI), American National Standards Institute (ANSI), and are referenced by the IBC building codes. Many municipalities require building permits for rack installations and require a PE stamped structural analysis be submitted with the permit application as specified by the building code.
How much load must the rack carry?
A racking structure must be analyzed by a structural engineer to determine if it can resist all applied loading in a given application. Loading not only includes the static weights of the stored product, but also impact loads, wind loads, snow loads, and acceleration loads from seismic activity. Engineers can determine seismic loads from American Society of Civil Engineers (ASCE) tools based upon the address of the planned installation site.

Will the rack design actually carry that load?

In evaluating a rack structure’s ability to resist the loads, the engineer will consider the gauge or thickness of the steel components, column shape and hole patterns, column backers, footplates, frame bracing panels, beam elevations, beam sizes, beam connection methods, bolted vs welded connections, and anchors. Also considered are the concrete floor and sub-soil. Engineers who specialize in pallet rack analysis are already familiar with the standards of most manufacturers and so will usually specify realistic designs consisting of standard catalog items often citing manufacturer’s model numbers.
In an application with used racking, the equipment already exists. The engineer then has to determine if the existing components will satisfy the structural design requirements and support all the loads.
But wait…
Can the specific design criteria of the used rack components be determined? Which manufacturer made the components, are the model numbers identifiable, and are the components designed to the current RMI specification? What gauge steel was used for each component? What are the weld specifications or frame bracing specifications? Will components from different manufacturers which look interchangeable actually fit together properly? Are any components damaged? Who is responsible for determining these factors and standing behind them? If the existing components can’t carry the loads, can they be modified to increase the capacity, and if so, who assumes the risk? Is there financial incentive to reduce or fudge the loading or safety factors to “make it work”? If there is a collapse with components from multiple manufacturers, where lies the liability? What are the hidden costs of these challenges and risks?


Mfg. Model Embossed Mismatched Components
Conclusion
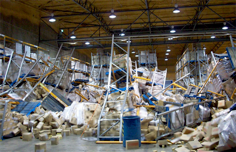
So, yes, used rack that meets the design requirements for a given application might be available in the marketplace, but the difficulty in verifying the construction of the components and the unfavorable shift of risk and liability bring out hidden costs that may make the deal a losing proposition.
Comments