A Field Guide to Racks
- Lisa Hemme
- Sep 25, 2017
- 5 min read
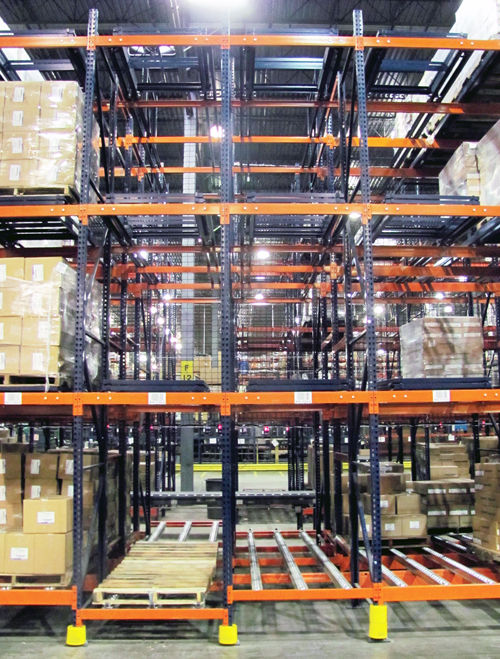
This quick and dirty primer on the most common types of pallet racks will help you determine which type is best suited to a particular application.
1. SELECTIVE RACK
If you're mentally picturing a rack right now, chances are you're imagining a selective rack. Featuring the most basic of designs—two upright frames and shelf beams placed between them. Walk into just about any distribution center or warehouse, and you're likely to see selective racking somewhere in the facility.
Selective racking is only one pallet deep, and racks can be placed either against a wall or back to back. In a single bay of selective racking, you can have multiple beam levels, with forklift trucks generally used to place the pallets on the shelf beams.
This type of pallet rack is called "selective rack" because it has a high level of selectivity, meaning that you can access every pallet in the racking system. The drawback is that the system does not provide as high a degree of storage density as other racking systems do.
Selective racks can be either welded or bolted together. The welded (or boltless) design is most popular in the U.S. due to the high cost of labor required to assemble racks on site and concerns around liability if the rack manufacturer is not directly involved in assembly. Bolted designs, however, are preferred when racks are being shipped long distances, particularly overseas.
Benefits:
More economical than other types of rack systems, with the lowest cost per pallet position
Can be easily reconfigured
Provides more selectivity and flexibility than high-density rack systems because pallets are not stored in front of one another
Does not require the use of specialized lift trucks
Applications:
Can be installed in just about any setting/environment and can be adapted to handle products of almost any volume, weight, or size
Well suited to product lines with low turnover and high differentiation
Good for operations with a high stock-keeping unit (SKU) count but low volume
2. DOUBLE-DEEP RACK
Double-deep racking is created by placing one row of selective rack behind another. The result is racking that's twice as deep as selective racking. In most cases, two pallets with the same product are stored in a slot, and a deep-reach lift truck or a lift truck with a double-deep handling attachment is required to access loads in the rear position.
While double-deep racking looks like selective racking, it is actually considered a type of high-density racking. High-density racking helps users optimize warehouse cube use by allowing more pallets to be stored per cubic foot. However, it is not as flexible as selective racking, and pallets are not as accessible. For example, in a double-deep rack, workers cannot access the rear pallet unless the front pallet position is empty.
Double-deep racking is made up of two rows of selective rack, one behind the other. A deep-reach lift truck or a lift truck with a double-deep handling attachment is needed to access loads in the back rack.
Benefits:
Cost per pallet position is lower than with other high-density options
Increases the productive use of floor space by 60 to 65 percent over selective racking
Applications:
Facilities that require high-density storage
Last-in, first-out inventory operations. Double-deep racking is not as suitable for first-in, first-out inventory management, as that would require double handling of pallets (removing the front pallet in order to access the back pallet)
3. DRIVE-IN/DRIVE-THROUGH RACK
Drive-in and drive-through racks are a type of high-density racking. They're designed so that lift trucks can enter the rack structure to deposit and retrieve pallets.
Drive-in and drive-through racks represent another type of high-density racking. They are designed so that lift trucks can enter the rack structure to deposit and retrieve pallets. The pallets are stored on rails that run the length of the rack, as opposed to on a shelf beam that's placed between two upright frames. These racks can store pallets two, three, or more deep.
Drive-in racks have one entry/exit point and therefore work well in operations that manage inventory on a last-in, first-out basis. Drive-through racks have an entry point on both sides of the bay and can be used in first-in, first-out inventory operations, as product can be loaded from one aisle and retrieved from the other.
It's important to note that because lift trucks are driven into these racking systems, these racks typically suffer more impacts than other types of racks do.
Benefits:
Requires fewer aisles than selective racking, increasing storage density
While the cost per pallet position is higher than with selective and double-deep racks, it is lower than with other high-density racking systems
Allows you to store up to 75 percent more pallets per square foot than with selective racking
Applications:
Works well for storing similar products on like-sized pallets
Suitable for high-volume SKU storage
Often used for freezer/cooler storage
Good for items that have a long storage life and don't require immediate access
Well suited to storing large quantities of relatively few product types
4. PUSHBACK RACKS
The rails of pushback pallet racks hold nesting carts that glide along the rails.
In pushback pallet rack systems, the pallet is placed on a series of nesting carts that glide on rails. New pallets are stored by pushing back the previously loaded pallets and placing the new load in the next cart position. Typically, pallets are stored two to six deep. When a pallet is retrieved, the next pallet drops forward into the ready position. As a result, pushback racks operate according to a "last-in, first-out" principle. Pushback racks do not require the use of any type of specialized lift trucks.
With a pushback rack, new pallets are stored by pushing back the pallets that are already there.
Benefits:
Provides similar storage density to drive-in racking's but with better selectivity and accessibility to a range of SKUs
Reduces picking time when a large number of pick faces are required
Provides higher utilization of available pallet positions than most storage systems do
Require fewer aisles than selective racking does
Faster to load or unload than drive-in racks are
Applications:
Operations that have a large number of SKUs and need a lot of pick faces
Bulk storage
Operations that store several products in quantities of more than five pallets per SKU
5. PALLET FLOW/GRAVITY FLOW
Pallet flow racks help make good use of space; they eliminate aisles.
Pallet flow racks usually feature a metal or nylon stop to keep the pallets in the bay.
In this type of high-density rack, pallet loads are placed at the end of a series of rollers or skate wheels and then flow down an incline to be picked at the opposite end. As a result, they are a first-in, first-out storage solution. Typically, there is a nylon or metal stop at the end to keep the pallets in the bay.
Benefits:
No limit to how deep you can go. Pallet flow racks that are equipped with a brake system have been known to go 20 pallets deep.
Maximizes space by eliminating aisles and storing pallets in lanes
Applications:
Works well in deeper systems
Can be used for pick modules and staging areas
Works well when you have a large volume per SKU
Good for high-throughput operations and for managing perishable and time-sensitive products
This guide has attempted to differentiate among some of the most common types of racking, but it is far from comprehensive. There are many other types of racks that we have not featured here. For example, cantilever racks store long or bulky items such as furniture, lumber, tubing, textiles, and piping. Carton flow racking operates like pallet flow racks but at the carton level. Mobile pallet racking mounts existing pallet racking or shelving on mobile carriages that move with the help of a mechanical-assist handle or an electric-powered system.
Comments